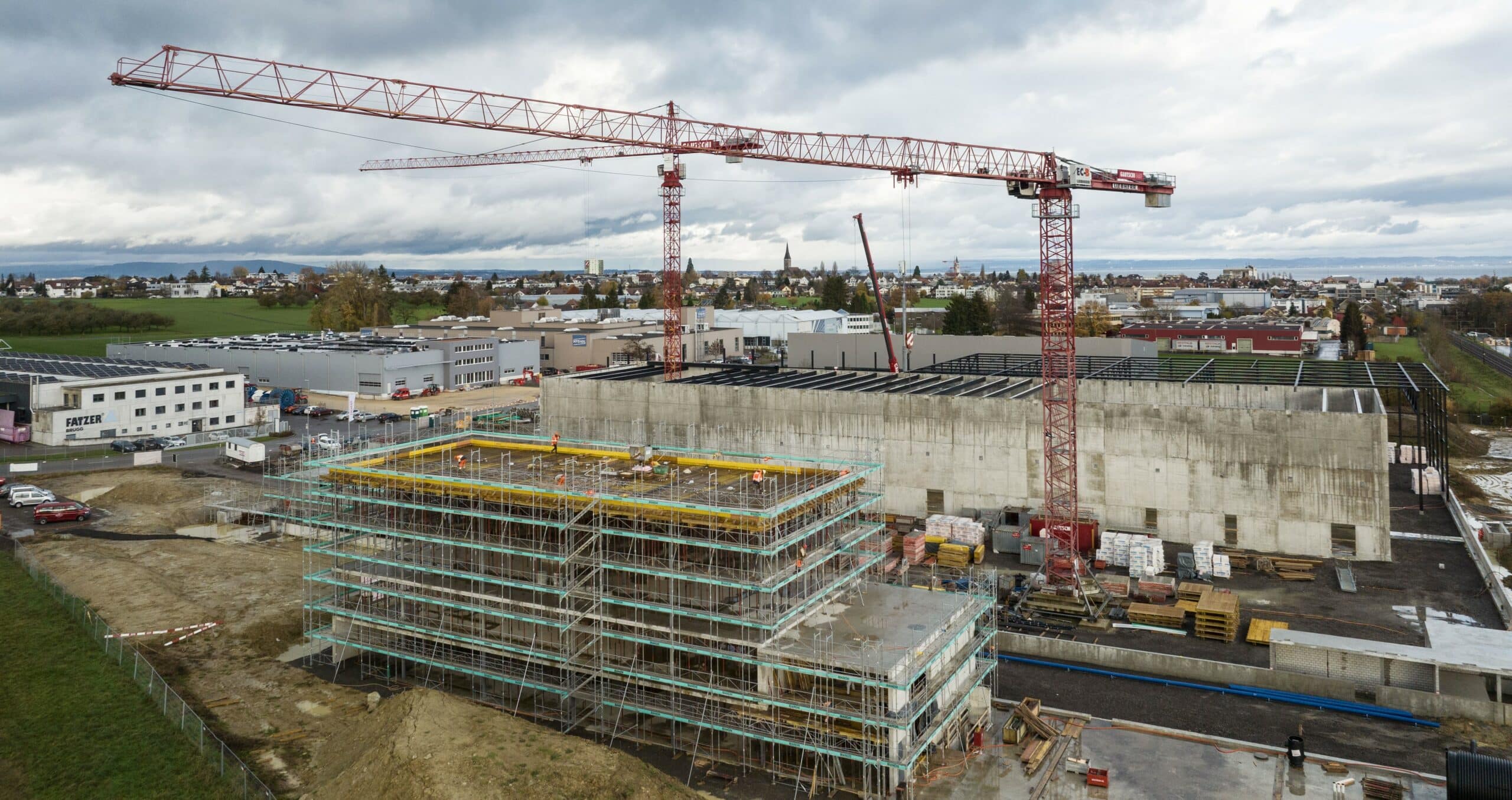
740 t d’acier d’armature pour le nouveau siège de Forster Profilsysteme AG
Le campus Forster certifié particulièrement durable
Forster Profilsysteme AG bâtit son nouveau siège à Romanshorn (TG). Le campus Forster est le premier complexe d’immeubles commerciaux de Suisse à recevoir la fameuse certification LEED Gold distinguant des constructions particulièrement durables. Debrunner Acifer Bewehrungen a livré 740 t d’acier d’armature à Gautschi AG, l’un des intervenants du chantier.
Forster Profilsysteme AG déménage à Romanshorn (TG) : le campus qu’elle y construit pour CHF 52 Mio sera son nouveau siège. Le campus Forster regroupera 140 collaborateurs auparavant répartis sur deux sites à Arbon. Il pose de nouveaux jalons de durabilité en matière de construction et d’exploitation. Pour ce projet pionnier du respect de l’environnement, Debrunner Acifer a notamment livré 740 t d’acier Green Steel.
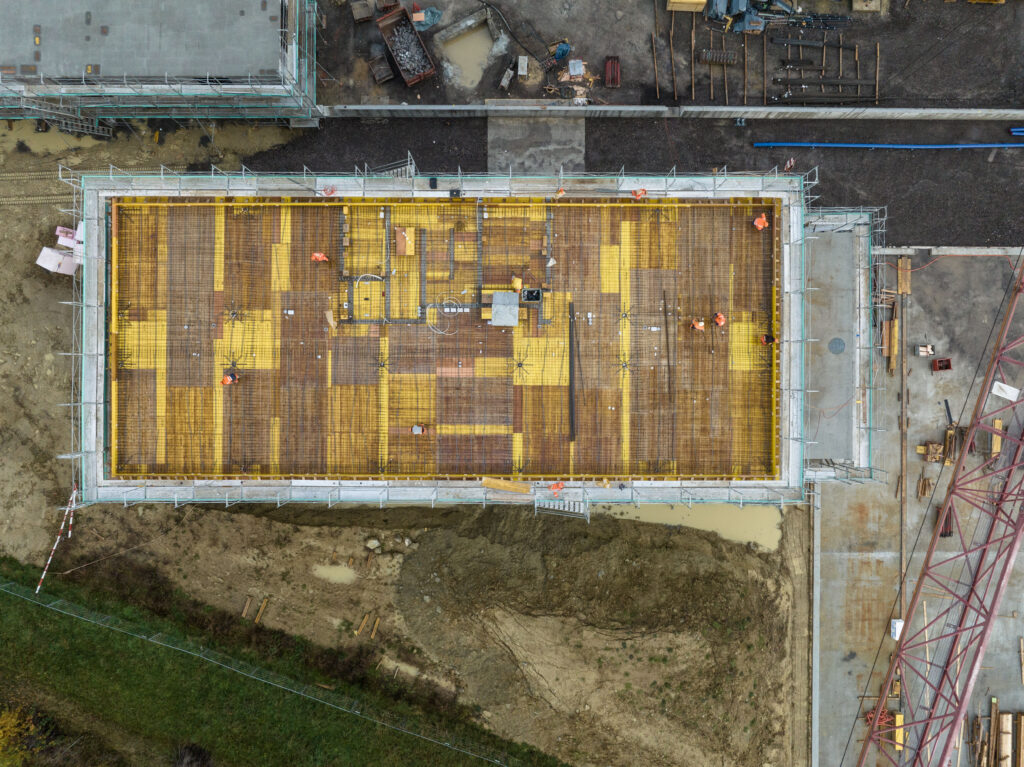
Trois bâtiments sur 30 000 m²
Le site de 30 000 m² accueillera trois bâtiments, chacun d’une hauteur d’environ 14 m. La halle de production et logistique de 11 700 m² comporte, entre autres, une unité de stockage en hauteur pour produits finis et semi-finis. Le deuxième bâtiment, tout en verre, abritera des bureaux, un showroom et des salles de réunion. Le troisième bâtiment, qui sera un centre technologique, comportera un centre de formation, un centre d’essais et un atelier de production.
Certificat LEED Gold pour les bâtiments particulièrement durables
Le campus Forster sera le premier complexe de bâtiments commerciaux en Suisse à décrocher le fameux niveau Gold de la certification LEED, qui distingue les constructions particulièrement durables. Forster Profilsysteme AG compte atteindre très vite un bilan CO2 neutre, voire positif. Les halles de production et logistiques et le bâtiment administratif sont déjà d’ores et déjà neutres en CO2. « Les toits du campus Forster sont quasi entièrement recouverts de panneaux solaires. D’une puissance de crête de 1,5 MW, ils alimentent toute la production en électricité verte. L’eau de pluie est récupérée pour les WC et l’irrigation des pelouses. Là où c’est possible, nous récupérons l’énergie résiduelle de nos processus pour augmenter le rendement du chauffage et de la climatisation », selon Willi Lüchinger, CEO de Forster Profilsysteme AG. Les exigences écologiques du maître d’ouvrage vont au-delà de l’exploitation du campus : la durabilité est un critère central déjà lors de la construction.
Acier d’armature : taux de recyclage minimal imposé
« Le label LEED fixe la part de métal recyclé de l’acier d’armature », explique Peter Spirig, chef de chantier chez Gautschi AG, chargé de la construction du bâtiment. « De plus, il faut déclarer d’où vient le fer recyclé ». La réduction de l’émission de poussière pendant le chantier faisait aussi partie de exigences LEED. Pour l’élimination des déchets, Gautschi a dû indiquer où les gravats, déchets et restes de matériaux d’isolation étaient amenés et ce qu’il en était fait. Même le béton était soumis à des dispositions spéciales.
Béton R : le seul conforme aux exigences LEED
Le béton conventionnel se compose de matériaux primaires telles que le gravier, le sable et ciment. Le béton préservant les ressources est entièrement ou partiellement composé de granulats recyclés obtenus par traitement des déchets de construction. « LEED exige du béton R et définit, en plus, la part de matériaux recyclés », explique Peter Spirig. « Dans la région, un seul fournisseur propose ce type de béton ». Gautschi AG a déjà utilisé du béton R pour d’autres projets, mais : « Avec plus de 5000 m3 de béton – 12 000 t – les quantités nécessaires pour le campus Forster dépassent nettement celles utilisées jusqu’à présent ».
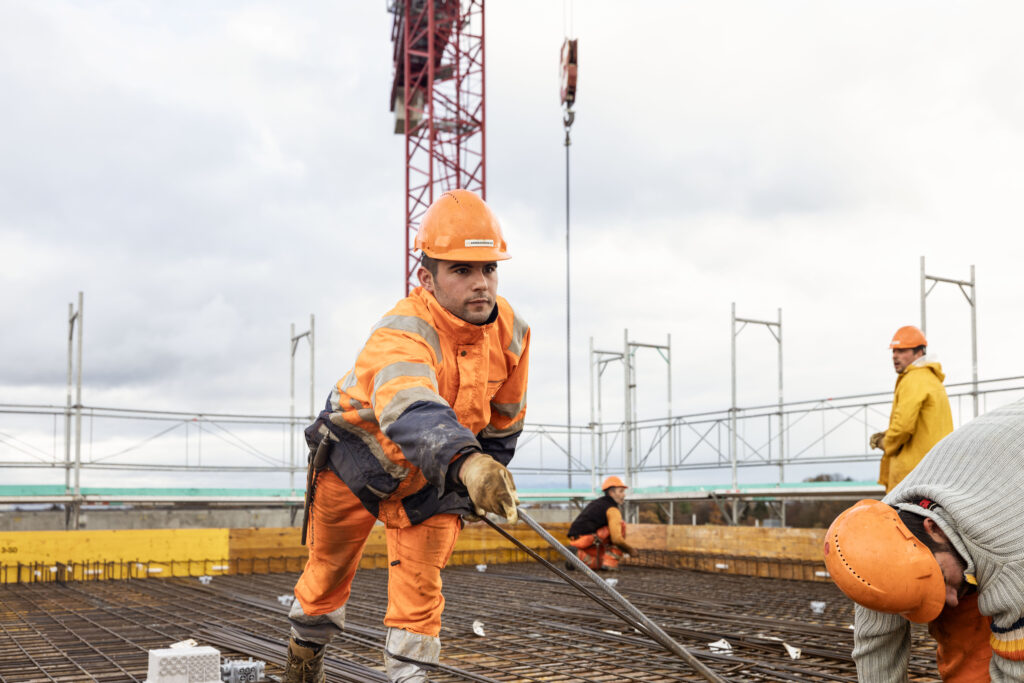
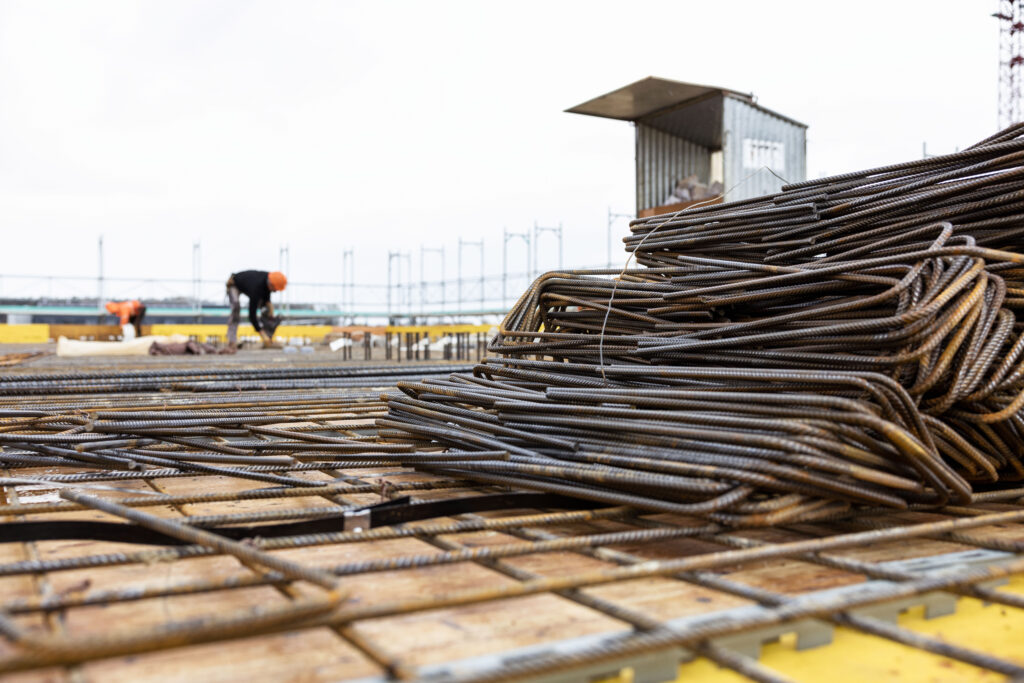
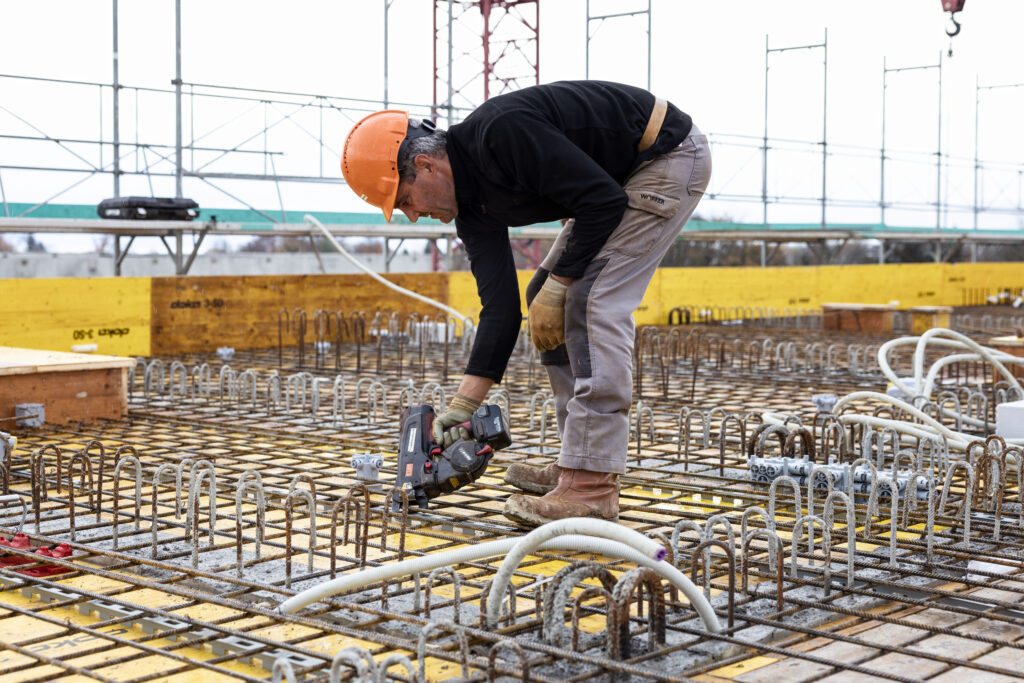
Stockage en hauteur : en 3 étapes jusqu’à 15 m de hauteur
Les travaux du bâtiment de 15 m de haut prévu pour abriter une unité de stockage en hauteur nécessitaient des règles de sécurité spéciales. L’ouvrage a été réalisé en trois étapes. Pour garantir la sécurité des collaborateurs, Gautschi avait contacté la SUVA déjà avant le démarrage du projet. « Pour la protection antichute, nous avons construit des tours d’échafaudage et les déplacer avec la grue de chantier. Le risque d’accident a ainsi été très nettement réduit. »
Inauguration pour le jubilé du 150e
Le campus Forster est un des plus grands projets de l’histoire de l’entreprise Forster Profilsysteme AG. Il sera achevé en 2024, pour le 150e anniversaire de l’entreprise et réunira passé et avenir dans une construction durable. Enfin, ce campus est un engagement clair et fort en faveur de l’économie suisse.
LEED Gold récompense les constructions durables
« LEED » signifie « Leadership in Energy and Environmental Design ». Ce label américain définit des standards de construction durable, avec les niveaux Platinum, Gold, Silver et Certified remis selon un système de points. Il évalue par exemple les critères suivants : consommation d’eau, efficience énergétique, qualité de l’air intérieur et extérieur, traitement et recyclage des déchets de chantier, mesures environnementales sur les chantiers, efficience énergétique, émissions annuelles de gaz à effet de serre (en équivalents CO2). |
À propos de Forster Profilsysteme AG
Forster Profilsysteme AG développe et produit des profilés de qualité en acier et inox, à longue durée de vie, pour fenêtres, façades et portes. Elle produit chaque année environ 3000 profilés différents pour les systèmes qu’elle développe et commercialise partout dans le monde. |
« Nous misons sur une économie circulaire »
Willi Lüchinger, directeur de Forster Profilsysteme AG
Pourquoi construisez-vous ce campus ?
En tant que locataires à Arbon, nous manquions de sécurité et d’indépendance à long terme, et notre dispersion sur plusieurs sites compliquait l’optimisation des processus et la collaboration des équipes. Nos possibilités de croissance étaient également limitées. S’y ajoute qu’à l’avenir, nous voulons assurer notre production et notre développement en privilégiant la durabilité, ce qui, en tant que locataires, n’était possible que de manière limitée. Enfin, cela nous permet de proposer des postes de travail prêts pour les exigences du futur, ce qui était difficile sur nos sites actuels.
À quels défis avez-vous été confrontés dans ce projet ?
La première tâche cruciale a été de trouver une surface suffisamment grande et déjà bien équipée. Nous voulions aussi garder le plus possible de collaborateurs/trices après le déménagement, et garantir le transfert de connaissances. Au cours de l’évaluation de plusieurs sites potentiels, la question de la rentabilité s’est également posée. Une fois tombés d’accord sur le site idéal (Romanshorn), nous préparions le lancement des travaux de construction quand on nous a soudain demandé un plan d’aménagement détaillé de tout le site. Nous avons dû reporter les travaux pour pouvoir le fournir, mais avons quand même réussi jusqu’ici à respecter le calendrier prévu. La crise sanitaire a aussi posé des défis en perturbant les chaînes logistique, et la guerre en Ukraine a fait exploser les prix. Mais contre vents et marées, nous avons maintenu le projet.
Les processus ont-ils changé ces dernières années ?
Nous avons compris qu’il fallait faire une croix sur le déroulement des projets d’autrefois – avant la pandémie. Le système « décidé le matin, livré l’après-midi » ne fonctionne plus. La gestion des coûts et du temps est devenue primordiale, surtout avec les prix élevés des matériaux. Une planification sûre, stricte et prévoyante est la seule solution. Grâce à une équipe compétente, nous sommes sur la bonne voie.
Quelle est la place de la durabilité chez Forster Profilsysteme ?
En tant que fabricant de systèmes de profilés, nous avons toujours été attentifs à la durabilité. Nous surveillons notre consommation d’énergie, utilisons des moteurs performants et sobres, réduisons les emballages en plastique et développons des matériaux d’emballage 100 % recyclables – pour ne citer que quelques exemples. En 2006, nous avons commercialisé le premier système de construction métallique entièrement en acier qui soit isolé. Sans autre isolant que l’acier lui-même, il est 100 % recyclable. Aujourd’hui encore, il est le seul système à rupture de pont thermique sur le marché entièrement constitué d’acier. En développant de nouveaux systèmes, nous donnons la priorité à la performance générale, mais aussi à l’économie circulaire.
La construction et l’exploitation du campus Forster intègrent-elles la durabilité ?
Nous sommes conscients de notre responsabilité en tant qu’entrepreneurs et employeurs, . Le campus Forster est un chantier pionnier de la construction durable et de la réduction des émissions de CO2.
Utilisez-vous vos propres profilés pour cette construction ?
Oui, bien sûr. Cela nous permet de mettre en scène nos systèmes durables en situation réelle. Et cela, avec une certification extrêmement exigeante.
Pourquoi avoir opté pour Debrunner Acifer Armatures comme fournisseur d’acier d’armature ?
Debrunner Acifer Armatures est un partenaire de longue date. Nous nous connaissons très bien. C’est un fournisseur performant et sérieux, avec lequel nous traitons de professionnels à professionnels. Cette commande était aussi une belle occasion d’entretenir ce partenariat.
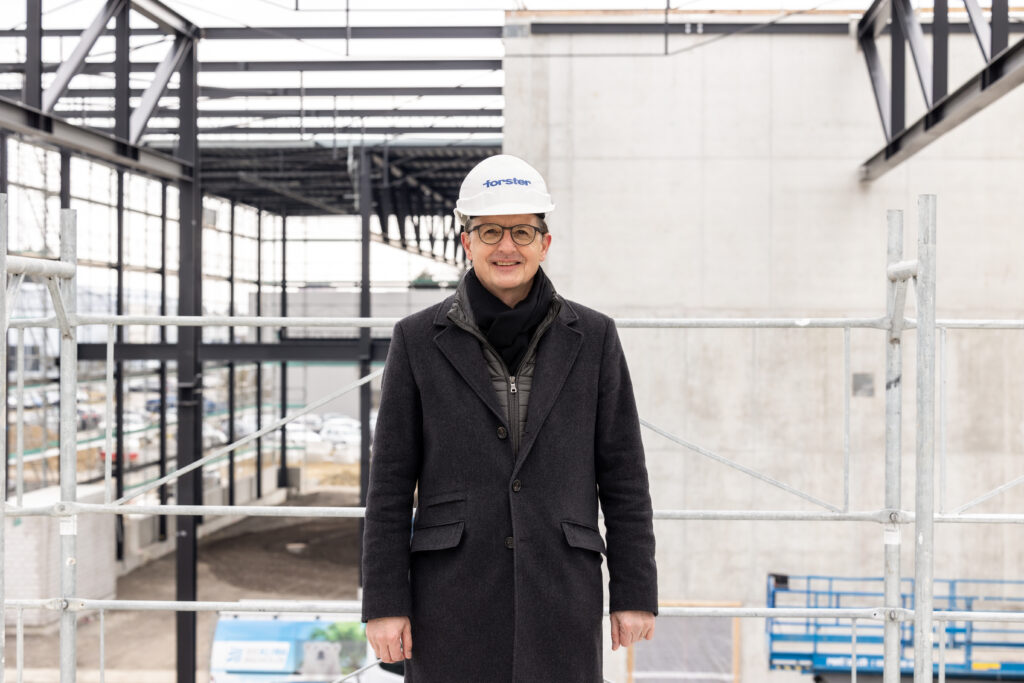
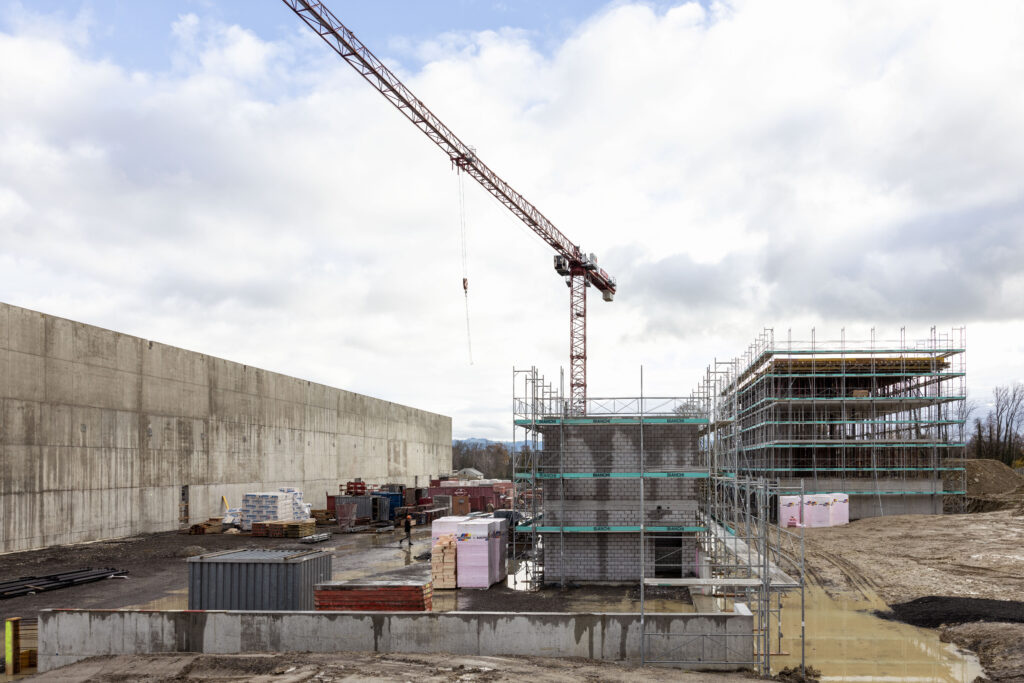
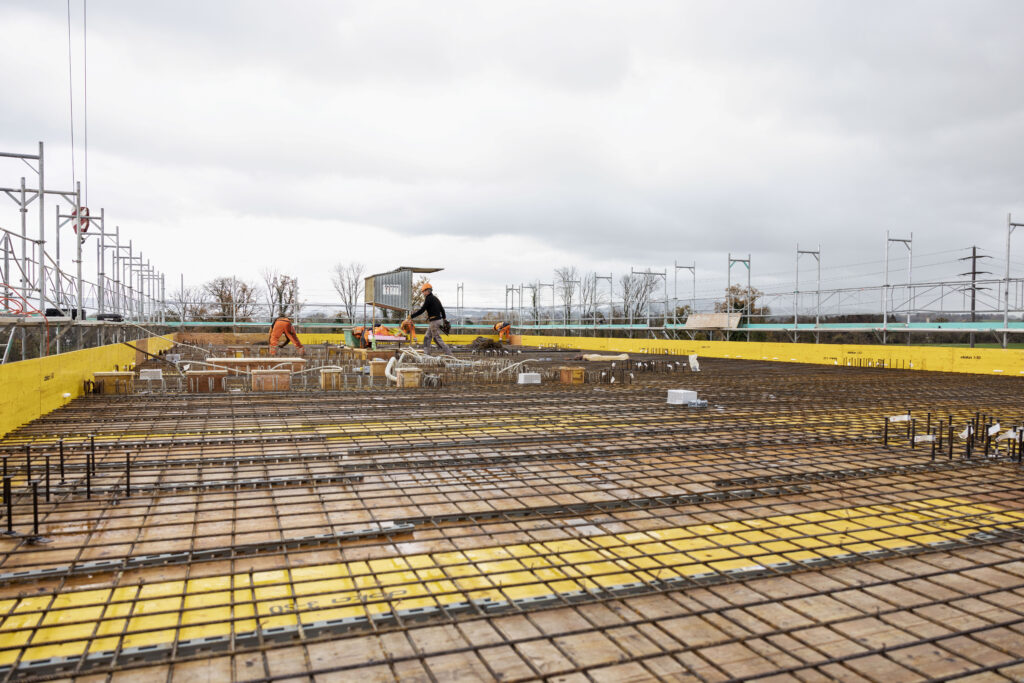
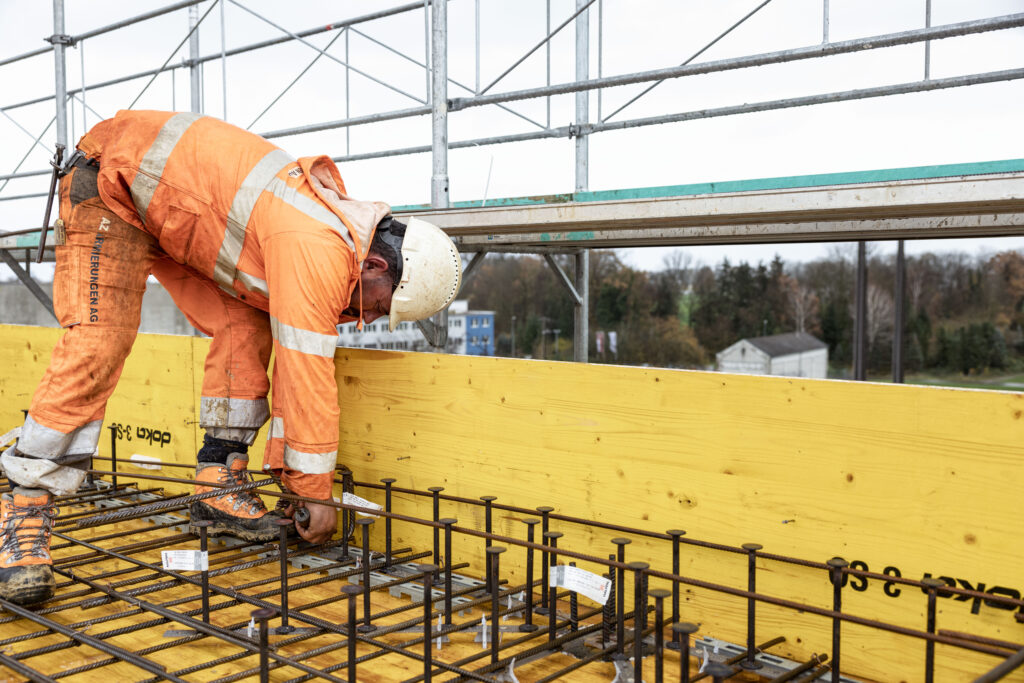
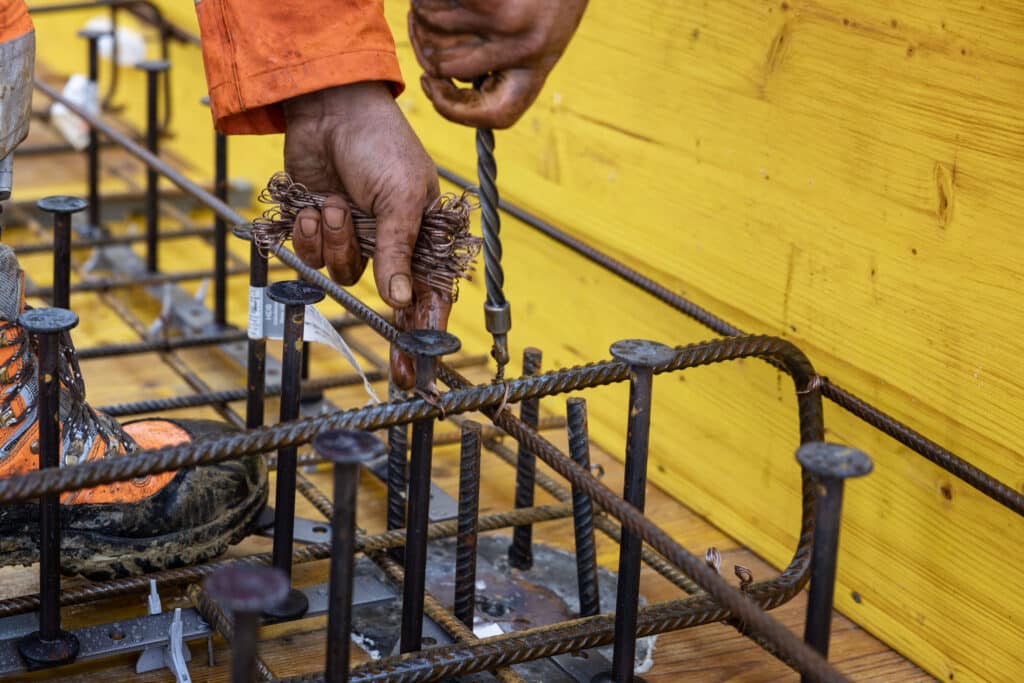
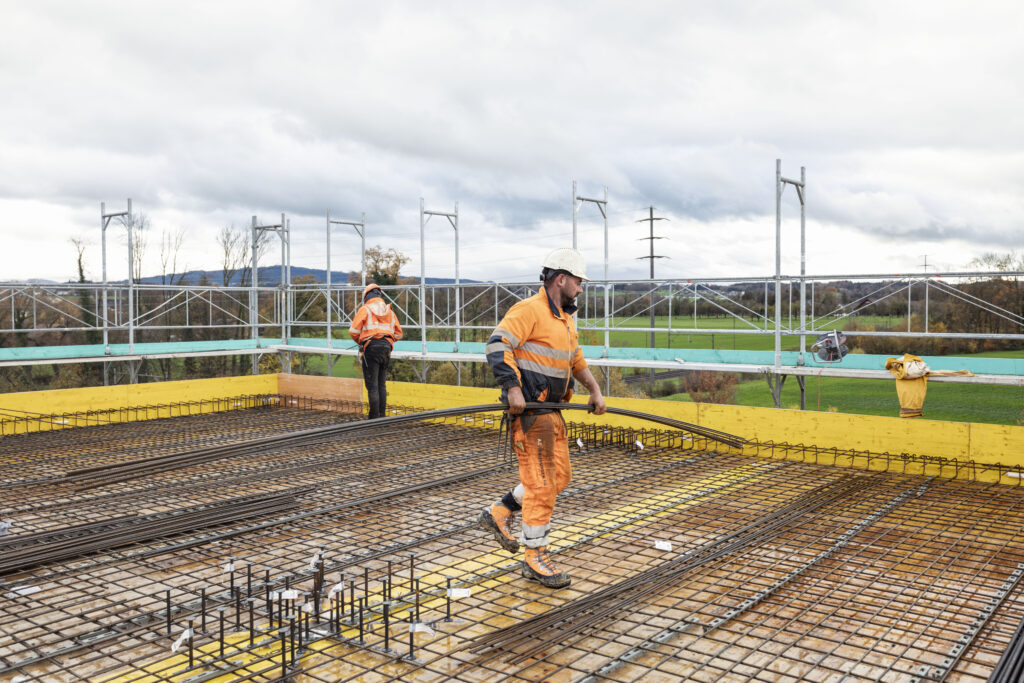
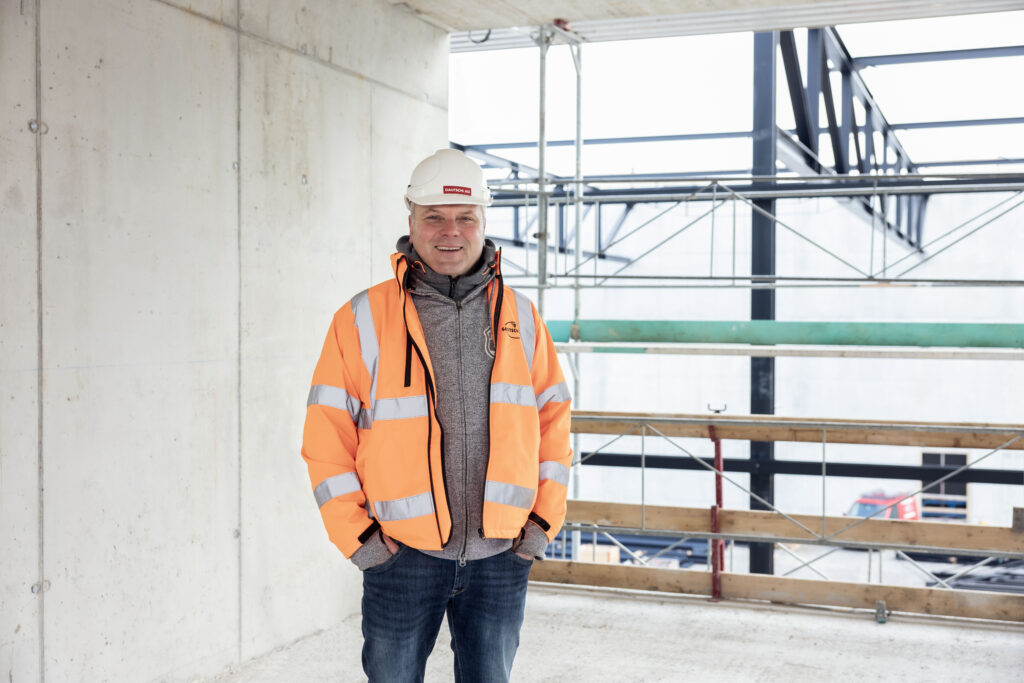
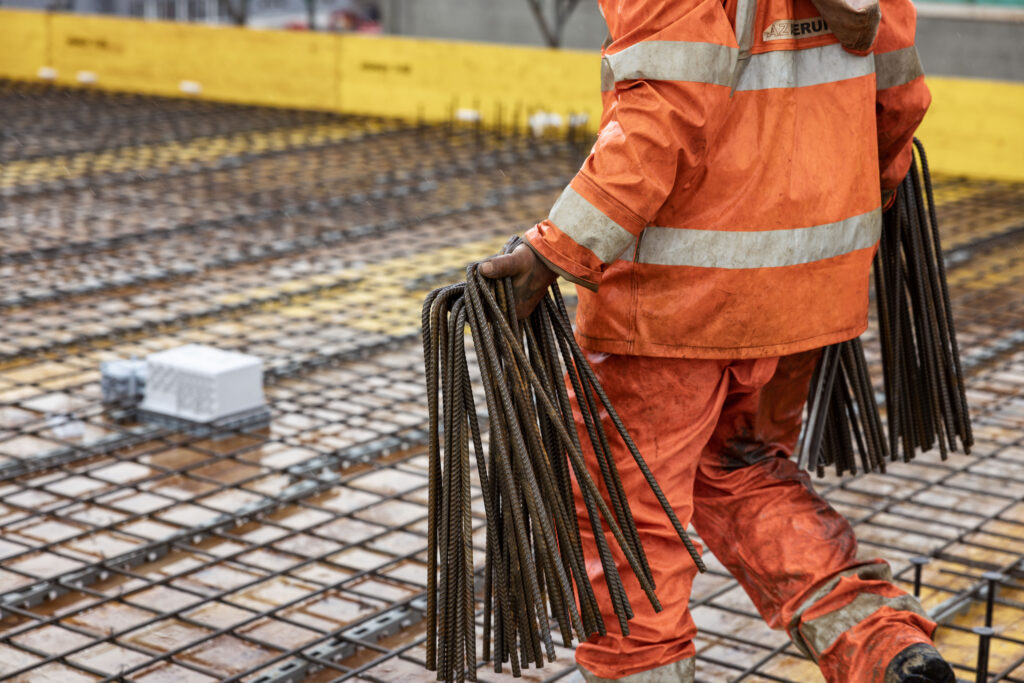
« Délais de livraison fiables »
Peter Spirig, chef de chantier, Gautschi AG
Êtes-vous satisfait du déroulement du projet ?
Globalement très satisfaits. Nous avons été épargnés par les accidents et avons pu respecter les délais. L’été chaud et sec a été éprouvant physiquement pour les collaborateurs du chantier, et ce n’était pas idéal pour la mise en œuvre du béton. Mais nous avons réussi à remplir notre mission.
Y a-t-il eu d’autres difficultés ?
La grande surface du chantier a rallongé les trajets, nécessité davantage de collaborateurs que d’habitude et nécessité trois grues au lieu de deux. La proximité des lignes à moyenne tension des CFF nous interdisait de placer les grues n’importe où. Il fallait tenir compte du périmètre de chute : aucune ne devait pouvoir toucher les lignes CFF, même en tombant accidentellement. Les directives LEED d’élimination du béton et de l’acier – avec le plus de recyclage possible – et de longueur des trajets ont nécessité des processus spécifiques.
Quel a été le facteur principal pour le bon déroulement du chantier ?
La planification avec le contremaître et la direction des travaux est essentielle pour un tel projet – relativement grand pour nous. L’étendue du site a nécessité d’aménager des pistes et des points de déchargement. Ces derniers devaient supporter 600 à 700 passages de camions transportant en tout 5000 m3 de béton. Notre contremaître a dû élaborer un programme sur 3 semaines précisant le matériau à livrer, la date de livraison, ainsi que la date et le lieu de pose. Rétrospectivement, c’est à ces mesures de planification que nous devons la réussite du chantier.
Êtes-vous content du service de livraison de Debrunner Acifer Armatures ?
Debrunner Acifer Armatures nous livre principalement de l’acier d’armature, des liaisons d’armatures et des armatures de poinçonnement. Nous sommes très satisfaits de leur service de livraison. Nous transmettions les listes de fers 14 jours avant le ferraillage et recevions généralement le matériel dans les 5 jours ouvrables. Nous pouvons confirmer la bonne réputation de Debrunner Acifer Armatures concernant la fiabilité des délais de livraison.
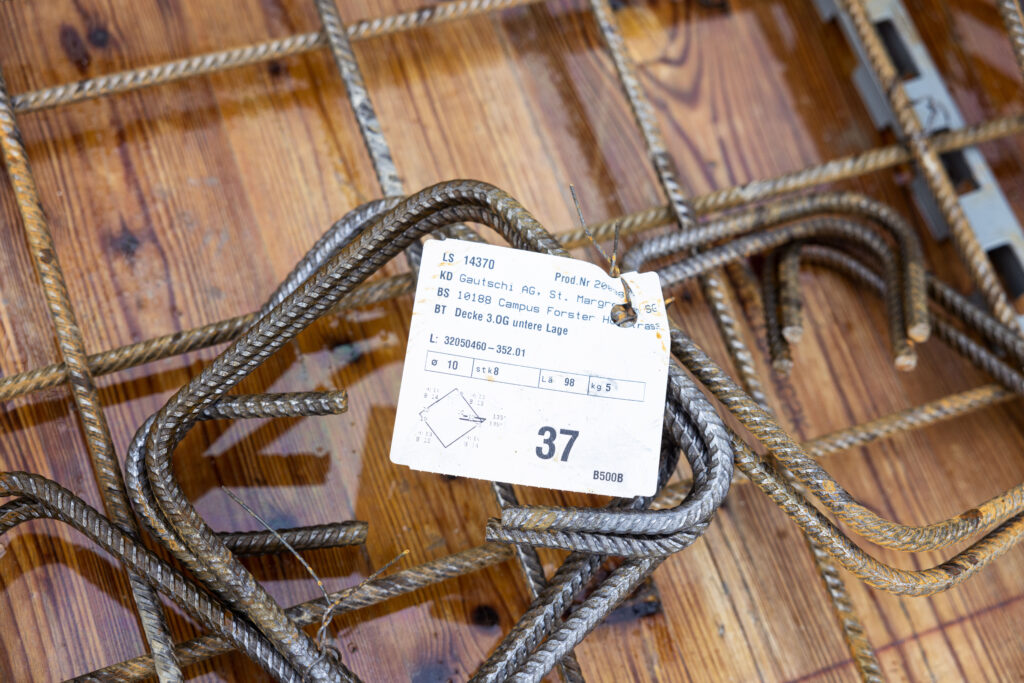
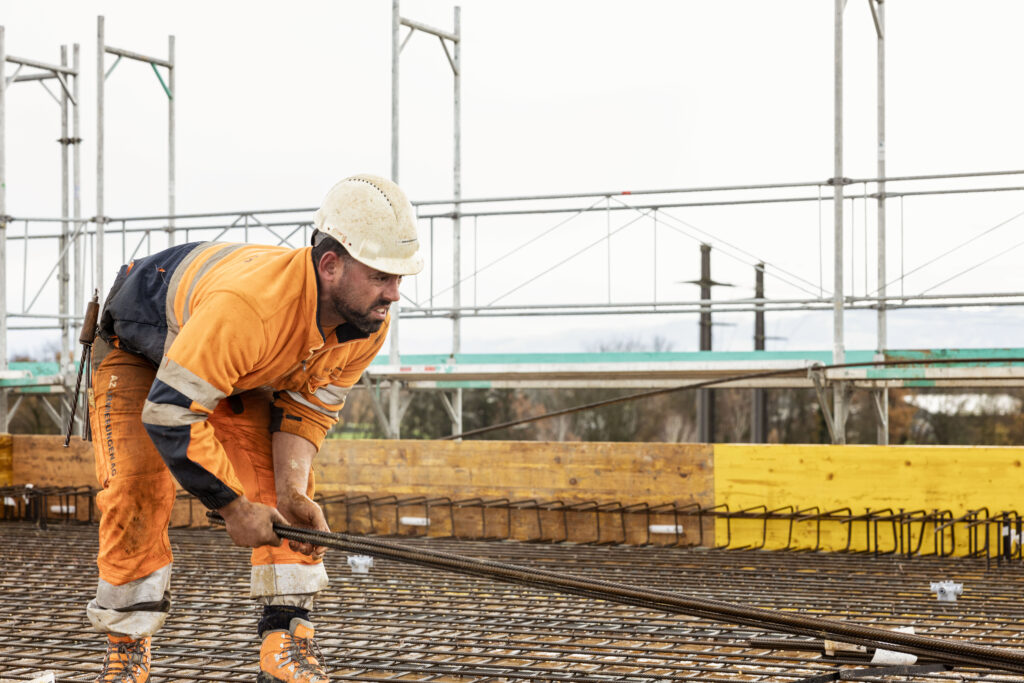
Maître d’ouvrage: | Forster Profilsysteme AG, Arbon |
Architecte: | Gisel + Partner AG, Arbon |
Bureau d’ingénierie: | Wälli AG Ingenieure, St.Gallen |
Entrepreneur général: | Gautschi AG, St.Margrethen |
Durée du chantier: | 2022 – 2024 |
Superficie du campus: | 30’000 m2 |